引言
航运业面临温室气体排放量日益增加[1]但国内外碳减排法规政策日趋严格的现状,绿色航运业已成为当前新的研究热点[2]。为了应对温室气体持续增加的难题,航运业在双碳战略大背景下主要采取能源替代、节能增效及碳捕集、利用与封存等碳减排方式。绿色新能源技术的船舶应用是当前的热门发展方向,但是新能源还存在着成本高及技术不成熟等问题,缺乏满足全世界航运所需基础设施的能力。相较之下,常规化石燃料的动力系统、供应链及管理体系则更为成熟。到 2050 年,以重油、柴油及液化天然气(Liquefied Natural Gas, LNG)等化石能源燃料选择加成仍将占据全球船队的一半以上[5],故以化石能源为主的传统能源仍将是未来至少 30 年内船舶的主流能源。通过提升船舶能效以实现减碳的效果十分有限,不能匹配当今的碳减排压力,进而支撑减排目标。而碳捕集、利用与封存(Carbon Capture, Utilization and Sequestration, CCUS)技术是目前实现航运业碳减排的最有效技术之一,进行船舶 CCUS 技术研究势在必行。CCUS 技术在陆上电力、石油、化工等领域已开展商业试用,但在船舶中的应用还处于起步阶段,亟需开展船舶 CCUS 技术的研究和应用。本文总结了国内外船舶 CCUS 技术的研究进展,分析了 CCUS 关键技术在船舶上的应用方式;针对 LNG 船舶提出了 CCUS 系统的技术路线,总结并探讨了船舶 CCUS 技术目前存在的问题及发展方向,为促进船舶 CCUS 技术的发展与应用提供参考。
1 国内外船舶 CCUS 技术进展
国外较早开展了船舶 CCUS 技术研究,已经在船舶 CCUS 技术可行性、实施方案示范项目及装备研制上取得了一定的进展。其研究成果推动了船舶 CCUS 技术的发展,为船舶 CCUS 技术应用和推广奠定了理论基础。
1.1 国外船舶 CCUS 技术可行性研究
得益于陆上日益成熟的碳捕集、利用与封存技术,对于航运业碳减排,船舶 CCUS 技术被寄予厚望。Wang 等[9]通过实船试验和计算机仿真论证了碳固化法用于船舶碳减排的可行性,认为船舶碳捕集与封存是减少航运业温室气体排放的优秀方案。Wang 等[10]进一步研究了某散货船上采用固化法减排方案的运行成本及利润,表明CCUS 在船舶上应用的经济可行性,同时利用仿真手段证明了 CCS 安装在某集装箱船上的可行性。Fang 等提出了一种在严格的船舶能效营运指数约束下确定船舶CCS容量的优化配置方法,提出的模型第 1 阶段是确定 CCS 的容量和储能系统的扩展容量,以维持 CCS 的运行,第 2 阶段是一个联合的船上发电和需求侧管理模型,以解决 CCS 集成导致的电力短缺问题,研究表明:碳捕集系统是可再生能源成熟前减少船舶温室气体排放的可行替代方案。Stec 等[11]分析了包括SO2 脱除、碳捕集和 CO2压缩在内的整个船舶碳捕集系统的能量需求,根据热带及北极环境下的情景模拟,指出燃烧后碳捕集工艺是降低船舶能效设计指数的很有前景的技术。Ros 等指出在节油措施下其他减排方法不会产生较高的碳减排率,而船舶碳捕集技术可在短时间内实施并有可能大幅减少海运部门的碳排放量。Oh 等[12]认为新型船舶膜捕集和液化系统可以成为国际海事组织( International Maritime Organization, IMO)2050 年温室气体减排目标的一个极具竞争力方案。García-Mariaca 等指出船舶碳捕集和封存系统可能是实现内燃机驱动的运载装备零碳排放的较好选择,针对内燃机为动力的运载装备开展了碳捕集案例分析,结果表明在海运公路货物运输装备上运行 CCS 系统是可行的。Guirma 等认为基于船舶的碳捕集技术是减少大型海上 LNG 动力船碳排放的非常有效的方法,在满足边界条件下船东将有很大潜力实现IMO 2030 与 IMO 2050 目标。PMW Technology公司与切斯特大学等合作进行的一项研究表明:低温碳捕集过程在船舶上应用是可行的,同时可与工业集群开发的已有基础设施一同发挥有益协同作用,最大限度地减少了额外投资。
1.2 船舶 CCUS 技术路线及经济性研究
船舶 CCUS 技术路线的选择首要考虑的是高效、经济。船舶碳捕集(Ship-Based Carbon Capture, SBCC)能耗占据整个碳捕集与封存技术能耗的 70%以上[16-17],捕集率及能耗是评估船舶 CCUS 效率和经济性的关键指标。国外学者目前主要通过性能更优的溶剂或改进工艺等方式提升碳捕集率和降低能耗。Awoyomi 等[18]以氨溶液作为捕集溶剂进行的 SBCC 研究结果表明:船舶主机负载在 85%时,废气余热回收的 4 MW能量足以满足溶剂在 90~100 kg·s-1 的再循环流速下达到 70%的碳捕集率。Long 等[19]在以单乙醇胺(Monoethanolamine, MEA)溶液作吸收剂的 3 MW 柴油机动力船上实现了 87.4%捕集率,并在此基础上研究了在相同工艺配置下性能更为优良的混合溶剂和添加中冷、多级进料及热集成等改进工艺,以提高碳捕集率。Akker[20]针对LNG 船舶利用 LNG 的气化冷能及尾气余热进行了船舶碳捕集流程的概念设计,在保证载货能力及稳定性的基础上进行了配备碳捕集设备的LNG 船舶空间设计。Awoyomi 等针对总装机功率为 10.3 MW 的 LNG 船,研究了氨水作为捕集溶剂的碳捕集技术,分析了发动机负荷对碳捕集率的影响,并针对不同 CO2 捕集率做了经济性评估,研究结果表明:在 90%的捕集率下,每吨CO2 捕集成本至少是 117 美元,而废气余热利用是大幅降低捕集成本的有效技术,在 60%~90%捕集率范围内,废气余热都可以满足再沸器的能量需求。Luo 等首次系统研究了吸收型化学溶剂 MEA 在 3.5 万总吨参考货船上的 CO2吸收工艺设计。研究结果表明:由于 CCS 系统热电供应有限,碳捕集率仅能达到 73%,此时每吨 CO2捕集成本为 77.5 欧元。在添加燃气轮机作为公用能源设施后,碳捕集率上升到 90%,相应设备多消耗的柴油使得每吨捕集成本上升到 163.07欧元。Feenstra 等[23]针对柴油机动力船及 LNG船舶提出了以 MEA 和哌嗪(PZ)作为吸收剂,利用 Aspen Plus 模拟了利用废气余热能进行碳捕集的过程,并在不同碳捕集率下对碳捕集成本进行了经济性分析,研究结果表明:捕集率的升高需要设备投入成本增加,但 CO2 单位质量捕集成本会降低,当吸收溶液由 MEA 溶液改为解吸压力更高的 PZ 溶液时,船舶碳捕集成本也会降低。Ros 等[7]研究了 SBCC 的一般设计考虑因素(溶剂选择、热集成及船舶运动等),然后以DerisCO2 项目中一艘名为“Sleipnir”的 LNG 船为案例研究了 SBCC 的概念集成设计及经济性分析等,研究结果表明:碳捕集、液化环节并不会对船舶造成重大影响。MEA 溶液虽存在高能耗及易氧化降解的缺点,但其在海洋环境下安全系数高,是当前 SBCC 的首选溶液。碳捕集率随尾气温度上升而提高,而液化 CO2 的量同样随液化压力增大而增加。碳捕集率虽然随吸收塔的静态倾斜角度增大而降低,但海船运动造成的吸收塔摇动并未降低碳捕集率。
船舶 CCUS 技术经济性评估是关系 CCUS技术应用的关键研究内容,为了提高船舶 CCUS技术路线的经济性,一些学者针对船舶 CCUS系统中的环节进行了能耗、成本的优化设计研究。Lee 等[24]针对 CO2 液化、蒸发CO2 再液化及CO2 卸载过程进行了建模与仿真分析,研究了最佳运行工况;结果表明:液化工艺中的每吨 CO2压缩功率为 103.42 kWh。Seo 等建立了 CCUS系统的经济性评估模型,基于全生命周期成本从几种可调节操作条件(压缩、制冷等环节)进行了优化,并将模型应用于 2 个案例中,研究结果表明:运营成本在全生命周期成本中占主导地位,其主要受液化系统的影响。用于液化驳船的成本随 CO2 运输规模增大而上升,而船舶 CCS链的总成本并未随 CO2运输船规模增大而降低。Seo 等[26]从 SBCC 的全生命周期成本出发评估了CO2 临时储罐的最佳容积。有研究人员从 CO2吸收溶剂、膜系统、碳捕集系统尺寸等方面对经济性的影响也进行了相关研究。Zhou 等[27]利用NaOH 吸收废气中的 CO2 形成 Na2CO3,再利用Ca(OH)2 溶液处理形成可带来经济价值的固体CaCO3,提供了新型、经济且更具紧凑性的船舶固态碳存储方案。Oh 等[12]考虑到 LNG 船舶尾气中 CO2 体积分数低(约 3%)及 O2 摩尔分数较高(约 16%)的情况,研究了适用于船舶的紧凑、节能的膜捕集及液化系统,并与胺基系统在能耗及尺寸方面进行了比较。Güler 等[8]通过工艺模拟手段研究了吸收塔水力设计参数对溶剂型CCS 系统效能的影响,并对油船、Q-Max、Q-Flex型及传统 LNG 运输船的 CCS 系统进行了成本对比分析,研究结果表明:在具有高速度及运费价值的 Q-Max、Q-Flex 型 LNG 运输船上,相较于航速控制、LNG 燃料使用等碳排放控制手段,CCS 技术更具成本效益。
1.3 船舶 CCUS 项目
除上述理论和试验研究外,国外还开展了船舶 CCUS 应用和示范项目,进一步推动了船舶CCUS 技术的进步。
2010 年,挪威船级社与 Process Systems Enterprise 公司合作开展了 Eurostar 的项目,该项目成功提出了一种用于船上 CO2捕集、液化和临时存储的概念设计 ,能够实现碳减排约65%。该方案利用化学吸收法从船舶柴油机尾气中捕集 CO2 并液化存储,然后通过港口进行转运。
2019 年 12 月,日本邮轮集团、Ardmore 造船厂、韩国大宇造船等共同发起 decarbon ICE 项目,探索 CCUS 技术在船舶上的应用。该项目面向新建船舶或改造已有船舶,预计能够减少90%以上的温室气体排放。该项目以已知的物理原理和技术为基础,可与新的碳中性燃料(生物燃料或合成燃料)相结合,以根除大气中的 CO2排放来源,最终实现负碳航运效果。采用低温处理技术将 CO2 制成流线型干冰,然后进行海洋封存。其中海洋封存的技术路线如下。
(1)利用低温处理技术将捕集到的 CO2制成干冰粉。
(2)利用成型设备将纯干冰粉制成质量约1 t 的流线型干冰。
(3)将流线型干冰抛投入海并深埋入海底沉积层。
(4)液态 CO2(干冰融化形成)和水反应生成 CO2 水合物,能够稳定存在于沉积层中,可以达到至少数万年的封存效果。
日本川崎 K Line 于 2020 年 8 月 31 宣布与三菱造船公司和日本海事协会合作 Carbon Capture on the Ocean(CC-Ocean)项目[32]。该项目进行紧凑型碳捕集装置的开发,并验证海上碳捕集装置的可操作性和安全性,探索海上碳捕集系统的紧凑性要求及稳定运行的规格要求[33]。CC-Ocean项目于2022年完成了全球首次海洋船舶碳捕集的示范研究,在一个输出功率为 8 500kW的89 000 DWT级运煤船上安装了50 m(35 m(长)×2 m(宽)×5 m(高))的碳捕集系统,完成了近 6 个月的实船测试验证。
油 气 行 业 气 候 倡 议 组 织 ( Oil and Gas Climate Initiative, OGCI ) 与 能 源 船 运 公 司StenaBulk 基于沙特阿美(Aramco)成功在重卡上进行碳捕集示范的经验,围绕船舶碳捕集技术进行了可行性合作研究。项目主要是评估船舶碳捕集技术可行性和经济性能,目标是为航运业2050 年比 2008 年降低 50%排放提供技术方案。
挪威航运公司 Solvang ASA 与瓦锡兰废气净化系统部门于 2021 年 10 月签署意向协议,计划在一艘 21 000 m3 乙烯船“Clipper Eos”号上进行 CCS 系统的全面试点改造安装,目标是实现未来深海船队的零排放。瓦锡兰废气净化系统部门基于脱硫系统设计了船舶 CCS 系统,2022年基于已有的溶剂研发基础完成了船舶碳捕集系统最佳吸收溶剂的选择测试。在总部挪威莫斯建立了 1 MW 陆上测试系统,初步测试表明可以实现 70%的 CO2 捕集率,原计划于 2023 年试点CCS 系统安装在“Clipper Eos”号上[35-36]。
挪威海工龙头企业 Aker Solution 于 2020 年8 月宣布剥离碳捕集技术相关业务,成立专业碳捕集公司 Aker Carbon Capture。目前该碳捕集公司已经完成了模块化的碳捕集系统,可灵活组合以满足不同规模的碳捕集要求,解决方案、服务和技术涵盖了整个 CCUS 价值链。
荷兰海事技术公司Value Maritime开发的首套 CO2 捕集模块和 CO2 电池于 2021 年 10 月安装到了 Visser 航运公司的 1036 标准箱集装箱船“Nordica”号上。该公司将 CO2 捕集模块集成到一种小型预制、预安装、即插即用的气体清洁系统——Filtree 系统上。该系统可以将捕集的CO2 充入电池,而此 CO2 电池是一种可以无限次充放 CO2 的存储设施。CO2 电池可以供给岸上CO2 客户进行利用,CO2被排放后可以将 CO2 电池再次运回船上充入船舶捕集到的 CO2。
韩国大宇造船于 2022 年 10 月 7 日宣布已经把碳捕集存储设备搭载在实际 LNG 运输船上并完成了性能测试。该船舶碳捕集系统通过 NaOH溶液将船舶废气中的 CO2 转化为矿物,然后将NaOH 再生重复利用。
目前已有的船舶 CCUS 示范项目都是通过燃烧后捕集技术手段实现船舶尾气的 CO2 减排处理,如表 1 所示。自 IMO 于 2018 年提出全球首份船舶温室气体减排初步战略以来,船舶CCUS 项目明显增多。目前来看,船舶 CCUS 项目的实施进展与预期计划还存在差距,同时其试点性使得投入比较大,亟需通过技术进步及规模效应降低其成本。船舶 CCUS 装备的开发研究刚起步,须推动船舶 CCUS 装备研究和应用进程。

2 国内船舶 CCUS 技术进展
相比国外已经较成体系的研究,国内船舶CCUS 研究存在差距。
2.1国内船舶 CCUS 技术可行性研究
李鹤鸣等分析了燃烧前、富氧燃烧、燃烧后等碳捕集技术在船舶上应用的优缺点,认为CCS 技术受限于成本及技术等问题而离在船舶上广泛应用还有一段距离。孙化栋等[41]同样针对CCUS 关键技术在船舶上的应用可能性进行了分析,总结了目前船舶 CCUS 存在的安装改造困难、捕集及存储成本高昂、存储与运输安全性关注不足等问题,并从 CCUS 技术进步、多能源耦合利用及政府政策方面提出了解决方案。金鼎从 CCUS 技术出发分析了船舶 CCUS 关键技术的应用前景,认为船舶碳捕集与封存部分关键技术已有突破,但还未到商业应用阶段。丁仲礼[43]肯定了碳捕集与封存技术在固碳减排方面的巨大潜力,但认为该技术仍需要继续研究。马永生建议加强 CCUS 产业顶层设计,加强关键核心技术攻关,推动 CCUS 产业链示范及商业化应用。马玉璞[45]根据中国碳源、碳汇分布国情指出海上碳捕集、利用与封存是实现电力及工业方面“碳中和”的可行技术选择及重要手段,发展海上碳捕集、利用与封存装备潜力巨大。李阳等[46]指出 CO2 捕集、利用与封存技术是中国实现“碳达峰、碳中和”目标技术组合不可或缺的重要构成部分。简炎钧[47]表示,CCUS 技术的经济性在一定程度上取决于后续的碳排放费用,未来随着航运碳排放市场机制的逐步发展,越来越高的碳排放成本将会提升 CCUS 技术的市场竞争力,并随着应用增加进而促进技术进一步成熟发展,降低设备制造成本,带来相关配套设施的完善,进而降低营运成本。
2.2 国内船舶 CCUS 项目
中国船舶集团有限公司第七一一所(七一一所)提出了主要包括船舶碳捕集、分离、液化提纯、利用存储等几个方面的总体技术方案,如图1 所示。通过吸收塔、解吸塔等设备实现船舶尾气中的 CO2捕集分离,然后进行压缩、干燥等工艺以液化存储 CO2,液态 CO2 可以交由 CO2 运输船进行陆上化工利用,也可以制成干冰进行海洋封存。

七一一所结合原有船舶脱硫塔设计基础开展碳捕集封存技术及实船示范验证研究,致力于船舶脱硫脱碳一体化处理的实现。七一一所于2022年1月份所获得了中国船级社颁发的全球首份船舶CO2捕集与存储系统原理性认可证书。其研制的船用CCS系统采用燃烧后捕集方法中的化学吸收法,考虑到船舶运营空间,系统高效、紧凑,还可以根据实际减碳需求进行碳捕集率调节。七一一所围绕高效吸收、低能耗、高紧凑性3个核心方向重点开展了CO2高效捕集、低能耗分离液化封存、脱硫脱碳一体化技术研究,完善技术链。此外,七一一所还针对低速机开展了 CCUS系统试验样机研制与验证,并对技术方案进行了优化。七一一所计划选择典型远洋船舶开展实船样机研制与示范验证,对系统实船适用性、经济性、可靠性等开展长期验证。
香港华光海运联合法国BV船级社同七一一所针对华光船队在役运行的2艘散货船签署了一份关于“碳捕集装置在运营船舶的应用研究”的合作协议。七一一所基于船舶设计方案设计定制化的碳捕集装置,而BV则依据现有法规和规范进行合规性检查,后续还将研究碳捕集装置在油轮上的应用。七一一所与山东海运股份有限公司也签署了船舶CO2捕集装置合作框架协议。中国船级社与江南造船(集团)有限责任公司、七一一所签署了“装备CCUS系统的新型低碳排放大型液化气船船型研发”技术合作协议,开展CCUS 技术应用于新型低碳排放的大型液化气船船型研发,积极推动CCUS技术的实船应用。
海德威科技集团(青岛)有限公司自主研发的船舶碳捕集与封存系统取得了挪威船级社和意大利船级社授予的原理认可证书。该船用碳捕集与封存系统能够满足船舶各种负荷工作条件,自主计算、调节CO2收集量以满足IMO规则对于现有船舶能效指数(Energy Efficiency Existing ship Index,EEXI)和碳强度指标(Carbon Intensity Indicator,CII)的限定值,如图2所示。废气经预处理单元及CO₂吸收及解吸单元处理后转换为清洁气体排出,而捕集的CO2随后进入液化及存储单元,实现液化存储,各单元间可通过换热单元实现能量阶梯利用。此外,还可以结合船舶空间特点进行CCUS系统各部分定制化布局设计,以适用于各种船舶空间。
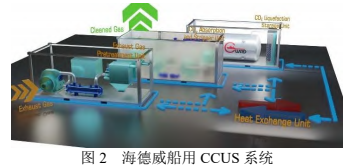
武汉理工大学和中海环境科技股份有限公司联合开展了干冰海洋封存的前沿性研究。包括干冰沉降过程其表面换热及相态变化过程分析及干冰沉降过程动力学研究;以降低干冰相变散逸损失、提升封存效果为目标进行干冰结构优化,设计了能够满足高效经济、绿色环保要求的干冰海洋封存装置。
总体来看,国外围绕船舶CCUS 技术在理论研究、项目立项及装备研发等多方面铺展,而中国关于船舶CCUS技术的研究及示范项目还比较少,也仅有极个别企业开展了船舶CCUS装备的开发设计,但船舶CCUS技术在“双碳”背景下正表现出强劲的发展劲头,将有越来越多的学者、企业投入到船舶CCUS 技术开发中。
3 CCUS 技术船舶应用方式分析
CCUS 技术虽在陆上初步实现了商业化应用,但无法直接应用于船舶。结合陆上应用经验和目前国内外船舶CCUS技术的研究现状,对几种典型CCUS中关键技术在船舶上的适用性进行分析,针对LNG船舶提出了CCUS 系统应用方案。
3.1 船舶碳捕集方式分析
船舶CCUS 技术中的首要环节是碳捕集过程。船舶运营具有离岸、不断移动、变工况等特殊性,因此,对船舶的碳捕集过程有特殊性要求。不同碳捕集方法的占用空间、能耗、技术成熟度、船舶改造量及投入成本等因素都会制约船舶碳捕集方式的选择,需要综合考虑各捕集方法的优缺点。
目前碳捕集技术从技术路线上主要包括燃烧前捕集、富氧燃烧、燃烧后捕集、生物质能捕集、直接空气捕集及燃料电池转换等方式。燃烧前捕集、富氧燃烧及燃烧后捕集较为成熟,而生物质能捕集、直接空气捕集及燃料电池转换为概念较新的技术。生物质能捕集是从生物燃料的燃烧或转化过程中捕集CO2的一项负排放技术,但其还面临着技术、经济及社会的挑战,还处于研发与示范阶段。直接空气捕集技术的显著优点是不受排放源种类和地理位置的限制,消除了在住宅区域及附近部署CCUS应用涉及的基础设施挑战,但还存在着成本较高的制约。高温燃料电池转换作为新兴技术可排除氮气进入工艺流,捕集CO2更为简便,但仍处于实验室研究阶段,具体碳捕集路径如图3所示。
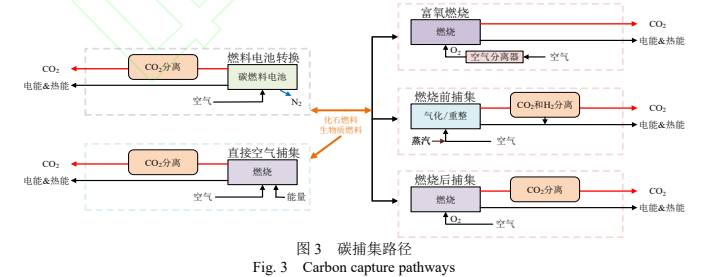
根据技术就绪水平将各种捕集技术划分为概念阶段、基础研究、中试阶段、工业示范、商业应用5个阶段。2021年国内外碳捕集技术成熟程度如图4所示。截至2021年,燃烧前捕集技术大多处于工业示范阶段,其中的燃烧前-物理吸收法已经可以商业应用。常压富氧燃烧技术已处于工业示范阶段,而增压富氧燃烧和化学链捕集法还分别处于基础研究和中试阶段。燃烧后捕集法中仅有化学吸收法达到商业应用阶段,其他燃烧后捕集方法多处于中试与工业示范阶段。国内在燃烧后-膜分离法、燃烧后-化学吸收法及燃烧后-化学吸附法上发展水平稍微落后于国外,而其他碳捕集技术达到国际领先水平。
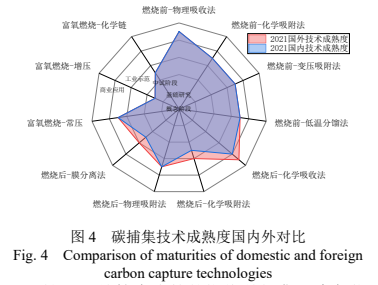
针对目前较为成熟的燃烧前捕集、富氧燃烧、燃烧后捕集等技术,主要从船舶改造量及投入成本、安全及稳定性等方面分析其在船舶上应用的适应性。
(1)改造量及投入成本。燃烧前捕集技术产生的氢气可作为船舶燃料,但需要开发船舶氢燃料发动机,解决船舶氢燃料发动机应用、氢气泄露及安全技术[6]等问题,还要进行动力系统整体设计改造并配备一些必备的反应罐及系统,改造量及投入成本巨大,在利用LNG燃料制氢使用LNG、氢气混合燃料船舶上发展潜力巨大。富氧燃烧受技术及设备的限制大,其在船上应用需要对船舶的发动机结构、系统及材料进行相关改造或升级,还需解决低成本的制氧技术及复杂的工艺设备问题,目前实施困难且应用机会小。燃烧后捕集方法只需对发动机废气处理系统进行改造,相比前2种方式改造量小,不需对发动机和动力系统进行改造,投资少[41]。
(2)安全及稳定性。碳捕集过程要安全,尽量避免高温、有毒等;相对于燃烧前与富氧燃烧技术,燃烧后捕集技术不需对燃烧过程进行改造处理,避免了高温及危险性操作过程,只需对产生的尾气进行处理,工艺更为简单。以MEA溶液为吸收剂的化学吸收法举例,其工作最高温度仅为120℃左右,能够较长时间稳定运行,其维护成本也远远低于前2种技术。
根据改造量、投入成本、安全及稳定性等评价指标,对上述碳捕集方法进行总结,见表2。
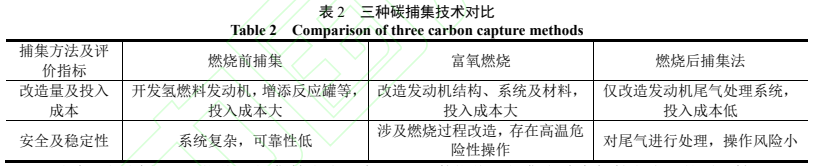
通过以上分析可见,燃烧后捕集技术应用在船舶上的改造量及投入成本低,而安全性及稳定性高,是最可能应用于船舶上的CO2捕集方法;目前国内外大都采用基于燃烧后捕集的技术路线开展船舶脱碳研究。
目前燃烧后捕集技术主要包括化学吸收法、物理吸附法、膜分离法、钙循环法、低温分离法等。采用燃烧后捕集必须要考虑船舶尾气的特殊性,需要针对船舶尾气的特点从燃烧后捕集法中选择合适的碳捕集方法。船舶尾气排放量大且成分复杂,含H2O、CO2、NOx、SOx及固体颗粒物等,且CO2浓度与分压低,如近年来订单量激增的 LNG船舶尾气中CO2摩尔分数约为3%[l2]。由于钙循环法中吸附剂的再生是利用燃料在富氧环境中燃烧产生的热量[58],其工艺也可以看为富氧燃烧捕集中的一种方法,因此,不再对其进行船舶应用的可行性分析。以下主要通过技术制约、紧凑性、能耗及经济性等方面分析其他燃烧后捕集方法在船舶上应用的适用性。
(1)技术制约。船舶必须采用合适、有效的碳捕集方法来保证足够的捕集率。采用物理吸附法CO2吸附选择性不高,分离效果较差。膜分离法对低浓度CO2分离效果差,还需开发适用于低浓度 CO2捕集的耐杂质膜材料。低温分离法也比较适合较高浓度CO2的分离,能实现高达99.17%的高浓度CO2分离[59]。相较其他方法,化学吸收法尾气适应性好且易工艺放大,是目前燃烧后捕集中最为成熟且得到广泛商业应用的方法[60-62],也是针对低浓度CO2捕集的最具竞争力的解决方案。面向船舶废气中低CO2浓度的情况,化学吸收法能够达到90%以上的碳捕集率。
(2)紧凑性。船舶本身运营空间有限,不能占用较多的载货空间,以免船舶经济效益受到影响。膜分离法紧凑性最为优异;变温吸附法系统体积大,发展较好的变压吸附紧凑性也受吸附床及压缩装置的限制;低温分离法所占空间受到压缩、冷却装置的限制;化学吸收法捕集装置紧凑性也存在不足,如醇胺溶液化学吸收法需要安装尺寸较大的吸收塔、再生塔及各种换热器等装置,通过微通道反应器、旋转填充床、电加热器替代传统的吸收塔和解析塔以提高系统的紧凑性是化学吸收法目前的发展方向之一。
(3)能耗限制。和陆地相比,船舶能源有限,需要充分考虑碳捕集装置的能耗,不能过多使用船舶能源。此外,能耗高则经济性不佳,不利于技术推广应用。物理吸附法能耗接近基准胺吸收过程中的再沸器能耗,每吨CO2捕集能耗约为2.89~3.59 GJ。膜法每吨CO2捕集能耗为1.96~2.85 GJ[67],能耗随CO2浓度降低而增大。低温分离法的压缩及冷却等环节耗能很大,改进工艺每吨CO2捕集能耗仍约为3.11 GJ[68],结合LNG 冷能利用是一个较有前景的发展方式[23]。化学吸收法中的吸收剂加热再生环节能耗大,醇胺吸收剂每吨CO₂捕集能耗可达4~6 GJ[55,69]。
(4)经济性。船舶CCUS 系统的建设除了考虑改造量及投入成本外,还需考虑运营成本的影响。物理吸附法所用吸附剂成本低,每吨CO2捕集总成本在40~63美元[70。但对CO2分压低于 15%的烟气处理不经济[71-72]。膜法每吨CO2捕集成本约为23美元,但分离膜的运维及换新成本高昂。低温分离法涉及到CO2压缩、液化环节,捕集分离成本很高,每吨CO2捕集成本约为32.7美元。;化学吸收法中胺溶液每吨CO2捕集成本为64.1~64.8美元。
根据技术制约、紧凑性、能耗限制及经济性等指标,总结上述各种燃烧后捕集技术,见表3。

综合分析各捕集方法的优缺点,尽管化学吸收法目前在空间紧凑性、能耗方面并不占优势,运营成本也不是最低,但其处理低浓度CO2性能最为优异,工艺也最为成熟,因此,在船舶碳捕集方法中脱颖而出。
3.2 船舶存储方式分析
CO2在船舶上捕集分离后,需要对分离出的CO2进行暂时存储。此外,通过船舶开展CO2运输对支持全球范围的CCUS至关重要[28],这也必然涉及到CO2的存储问题。存储方式的选取主要受船舶运营、后续运输、利用与封存技术的影响。船舶运输CO2的存储方式主要包括高压气态存储、液态存储及固态干冰存储。由于CO2液态存储具有成本低的优势,同时CO2液化成本在运输运营成本中占据较大比例,目前围绕液态CO₂船舶存储展开了较多研究。Seo等从CO2三相点和临界点间的7个液化压力出发,从船舶碳捕集的全生命周期成本中得出最佳液化条件下的压力和温度为15bar和-27℃,此时的每吨CO2处置成本为24.4美元。
船舶捕集的CO2在船舶上临时存储,需要考虑存储方式的占用空间与能耗、稳定性与安全性、技术成熟度与成本等方面。
(1)空间与能耗。高压气态存储方式会占据较大的船舶运营空间,但能耗较低。液态CO2体积仅为气态CO2体积的1/500[78],1tCO2在15 bar压力下的所占货舱体积约为2.4m77],而同等质量的CO2在CO2国标装气瓶中所占体积约为1020 m³(仅计算气瓶体积)。液态、固态存储在空间上占优势,但CO2液化、固化及维持相应存储条件都需要消耗较多能量,如泵和压缩机会消耗船舶的巨大电能。应当综合考虑空间与能耗间的均衡,使得船舶电力系统保持有足够的正常运行功率。
(2)稳定性与安全性。CO2存储的稳定性及安全性同样值得关注。海上极端天气频繁,CO2储罐或液舱内的CO2因温度极端变化引起的相态变化可能引起船舶航行的不安全问题。低温液态CO2泄露会对船体结构及人员造成损伤,液态CO2与海洋相互作用可能形成水合物和冰,温差会引起强烈的海流。部分未溶解的气体释放到大气中,在风速低及逆温影响下大气中的CO2可能导致船上人员窒息,还可能使得船舶引擎停止。储罐中的液态CO2产生的晃动效应可能会影响船舶的稳定性,降低航运性能。高压气态储罐发生罐体破裂、爆炸也可能会对船员的生命财产造成巨大损失。固态干冰升华后发生排出机舱内空气的意外事故,也可能使机舱船员面临窒息风险。
(3)技术成熟度与成本。目前以液态CO2存储的技术研究较多,液态CO2存储是最为成熟的方式,也是最具经济性的存储方案。干冰存储还仅仅停留在概念研究方面,未来会发挥更大的存储潜力。液态CO2在密相中具有高密度、低黏度的特点,通常通过多级压缩达到密相状态。此状态下 CO2存储体积小,所需运输压力低,使得船舶运输十分方便、高效[10],也有利于陆上通过管道方式运输。液化存储方式有利于下一环节即CO2利用或封存的进行,CO2的存储技术还可以借鉴LNG或LPG船的成熟经验,液化CO2技术路线实用性优势如图5所示。液态CO2可以使用储罐或集装箱进行船上存储,可以直接用作船舶上CO2灭火系统原料及制作循环燃料等,多余的液态CO2也可以由专门的液态CO2运输船或海洋供给船进行海上运输,一部分液态CO2可以用于海洋油气平台,其他的液态CO2可以经由陆上的管道、公路罐车、铁路罐车及内河驳船等运输工具进行化工利用或封存。
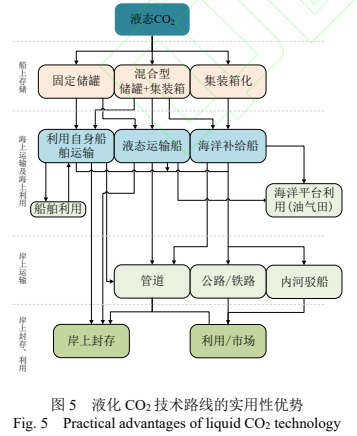
综合考虑存储的各个方面因素,未来以液态或固态CO2在船舶上存储的可能性更大,但需要探索更加节能、安全的CO2液化、固化及存储技术。
3.3 船舶 CO2利用方式分析
CCUS 技术在传统CCS技术上增加了利用环节,以期产生一定的经济效益,降低运行成本。目前CO2利用主要包括CO2直接利用与转化利用2个方面,CO2利用技术如图6所示。直接利用包括将CO2作为干冰、传热工质、制冷剂及食品工业应用,而CO2转化利用包括通过各种化学(如化学转化为燃料及化学品)及生物(如微藻固碳)过程将CO2转化为高价值产品。CO2资源化是CCUS 技术商业化发展的关键切入点,但当前商业化应用还主要聚集在地质利用方面。由于公众认知程度低、技术及资金获取难度大、项目运营风险大且收益慢、政策及运营体系不完善等原因,CCUS项目商业化进程缓慢。国外在地质利用、农业、尿素、甲醇、及食品级CO2利用上取得了商业化应用成果,但化学利用多处于工业示范阶段以下,而生物转化(制淀粉)、矿化利用甚至还处于概念及基础研究阶段。

结合船舶运营的特殊性探索船舶上捕集的CO2利用方式也是未来的一种发展方向。CO2可以为船舶CO2灭火系统提供CO2来源,一方面可以通过减少CO2气瓶的数量节省船舶的空间,另一方面可以减小船舶购买CO2气瓶的成本。CO2能够应用于海洋油气田的产量提升,同时也能够封存一部分CO2。海洋上运营的大量船舶的碳排放可以就近用于海洋油气田的处理,是发展潜力巨大的一种利用方式。我国已经研制出兆瓦级超临界CO2发电机组及超临界CO2循环发电装置试验系统,未来超临界CO2发电技术与CCUS 系统的联合是一个发展方向。
捕集的CO2用于去除海水中的溶解固体,生成船舶上的饮用水也是未来富有前景的利用方式。Ayyar等提出比传统热法与反渗透工艺更节能的催化海水脱盐法。有机胺RNH2与CO2反应产生不稳定的碳酸氢盐RNH3HCO3,利用RNH3HCO₃诱导与NaCl溶液(实验模拟海水)中的C交换生成RNH3Cl和NaHCO3,脱除的NaHCO3经酸性树脂处理提供的H实现CO2再生和Na+脱除。通过二胺或聚合物CO2响应性材料控制RNH3CI的溶解度,抑制水溶性NH4Cl的形成,实现进一步脱盐,最后碱处理不溶性RNH3Cl,使得RNH2再生,最终实现CO2与RNH2的循环利用,如图7所示。这不仅减轻了饮用水费用,还节省了船舶必需的淡水舱空间,有利于增大船舶载货空间,提高运营收益。
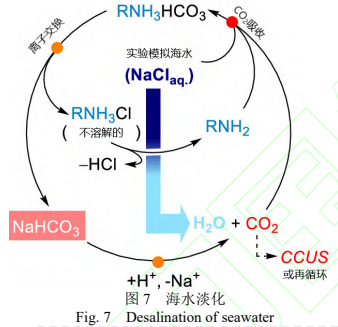
以CO2加氢制甲烷、甲醇为代表的CO2能源催化重整技术是资源循环利用的方式,制得的甲烷、甲醇为船舶提供能源是CO2利用的新选择。CO2加氢制甲烷或甲醇同时是解决氢气运输的一种方式。氢气在运输过程中风险很大,通过转化成甲烷或甲醇原料运输,到目的地再通过催化重整分解为氢气和CO2,CO2可以作为工业原料利用或者封存,而分解的氢气可以用作燃料。HyMethShip概念首次利用直接空气捕集的CO2和水电解产生的H2为原料生产电甲醇,电甲醇装载并存储于船舶上,船舶可以通过预燃系统(重整器)转换为H2和CO2,H2用于推动船舶,而CO₂ 被液化存储运输到电甲醇生产设施中并取代直接空气捕集的CO2用于电甲醇生产,该概念利用可靠的成熟技术使船舶推进系统具有一个几乎封闭的CO2循环,如图8所示。
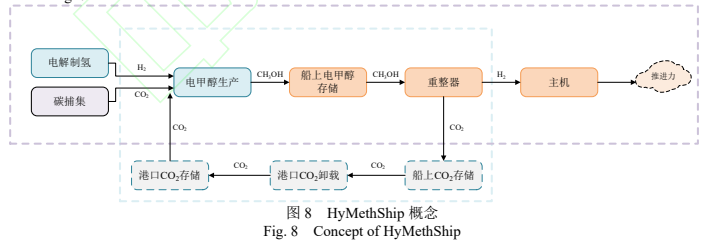
目前商船三井、日本制铁等九家日本企业成立的船舶碳回收工作小组正在评估生产和使用甲烷作为零碳排放船舶的可行性[87],致力于实现日本航运业温室气体零排放。瑞典循环碳能源公司Liquid Wind联合瑞士可再生能源生产商和能源交易商Axpo及能源技术公司Carbon Clean Solutions等多家企业开展的FlagshipONE项目正
3 焊接研究进展
目前殷瓦钢、5083铝和304不锈钢的焊接方法仍然以电弧焊为主,但是随着对焊接精度和焊接质量的要求不断提高,激光-电弧复合焊、激光焊、电子束焊以及搅拌摩擦焊等方法的研究越来越多。在开发液态、碳中性的绿色甲醇燃料。
通过催化环化等化学反应将船舶运营产生的CO2转化为增值化学品亦是未来的新兴方向。Iliuta等[88]提出了利用中型货船动力系统尾气中的CO2氧化苯乙烯生成苯乙烯环状碳酸酯(增值化学品)的想法,该研究表明苯乙烯环状碳酸酯反应器的紧凑性优势比公开文献中提到的通过吸收过程进行碳捕集的船舶装置更为显著,其技术路线如图9所示。
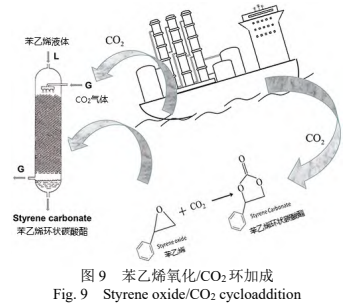
综合来看,虽然船舶捕集CO2用于海洋油气田驱油驱气仍是目前最具应用前景的利用方式,但CO₂能源催化重整、催化环化转换及淡化海水也将表现出来巨大发展潜力。